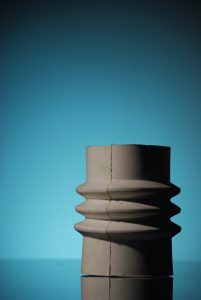
Casting is a common manufacturing process that involves pouring liquid material — usually material that’s been preheated — into a mold cavity. As the liquid material cools, it hardens to create a new object in the shape of the mold. The newly created object, known as a casting, is then removed from the mold and either used for other manufacturing processes or packaged and sold as a final product. Resin casting, however, is a unique casting process that’s characterized by the use of synthetic resin. To learn more about resin casting and how it works, keep reading.
The Basics of Resin Casting
As the name suggests, resin casting is a casting process that involves the use of synthetic resin. To better understand how it works, you must first look at the synthetic resin used in this casting process. Synthetic resin is any type of resin that’s converted into strong and rigid polymers via curing. In other words, it begins in a liquid state but converts to a solid state after being cured.
In resin casting, liquid synthetic resin is mixed with a curing agent — typically at room temperature or near-room temperature. Next, the two substances are poured into a mold cavity. The curing agent then converts the resin into rigid polymers, essentially hardening it. After this chemical reaction has finished, the hardened casting is ejected and removed from the mold cavity.
Advantages of Resin Casting
Resin casting is a simple process that can be performed using just a few basic tools and materials. In fact, many hobbyists use resin casting to create small objects. It’s a simple and low-cost way to produce small objects, making it a popular choice among individuals and hobbyists for leisure purposes.
Resin casting is also capable of producing objects in complex shapes. The shape of the casting is dependent upon the shape of the mold cavity. By using the right type of mold cavity, a manufacturing company — or a hobbyist — can create a casting in their desired shape.
Disadvantages of Resin Casting
On the other hand, resin casting is a poor choice for manufacturing companies looking to mass-produce a large quantity of objects or products. For starters, the synthetic resin used in this casting process is highly aggressive when exposed to a curing agent. As a result, molds typically only last for 50 to 100 uses, after which the mold must be discarded and replaced with a new mold.
Additionally, there are health concerns regarding the use of synthetic resin. During the curing stage, synthetic resins may release toxic and harmful fumes.