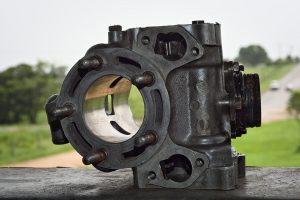
From engine blocks and cylinder heads to connecting rods and machine components, shell molding is used to make a range of different products. Also known as shell casting, it’s a relatively new molding process with origins dating back to the mid-1900s. Since then, it’s become a popular choice for manufacturing applications requiring extreme precision. So, what is shell molding exactly, and how is it performed?
The Basics of Shell Molding
Supporting both ferrous and non-ferrous metals, shell molding is a molding process that’s characterized by the use of a sand-base mold. Companies don’t use just regular “beach” sand for this process, however. Instead, a special type of resin-covered sand it used in shell molding.
Benefits of Shell Molding
Shell molding offers several benefits for companies, some of which include the following:
- Ability to create complex shapes with extreme precision
- Low labor requirements
- Supports most metals, including iron, steel, aluminum, copper and alloys
- Bubbling isn’t a problem since the mold is free of moisture
- Can be scaled for mass production
How Shell Molding Is Performed
Although it requires minimal labor, shell molding is a somewhat complicated process that requires multiple steps. First, the sand is thoroughly mixed with resin, which acts as a binding agent. Next, the sand is poured into a heated mold — with the mold typically reaching temperatures of 400 to 700 degrees Fahrenheit. A heated mold is important because the heat triggers a reaction with the resin-covered sand. When the sand comes into contact with the hot mold, a shell is formed on the inner surface of the mold.
After the shell has been formed, any excess sand is removed from the mold and either discarded or saved for other applications. The shell is then removed from the mold, which typically occurs using ejector pins. The ejector pins are built into the mold itself, allowing companies to easily remove the newly created shell without damaging it.
In Conclusion
Shell molding is a molding process invented by German engineer Johannes
Interested in the different molding processes? Learn more about dip molding here.