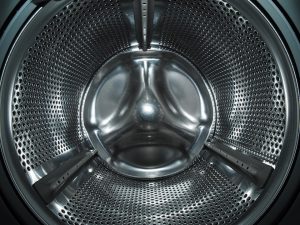
It’s not uncommon for metal objects to feature a chemically treated surface. Electropolishing is one such process that uses both chemicals as well as electricity to treat the surface of metal objects. Also known as anodic or electrolytic polishing, it’s used by manufacturers to create a smooth surface on metal objects. Unless you’re familiar with electrochemical processes, though, you might be wondering how electropolishing works.
The Basics of Electropolishing
To perform electropolishing, a metal object is submerged in an electrolyte chemical-filled container that’s connected to a power supply. When the power supply is activated, it triggers a chemical reaction that levels ridges and valleys on the surface of the metal object. Basically, electropolishing serves as a catalyst for oxidation, which dissolves the surface of the metal object. As the surface begins to dissolve, it leaves behind a smoother and more uniform surface that’s often preferred by manufacturers. Non-level imperfections on the surface of the metal object are dissolved into the electrolyte chemicals, leaving behind a smoother surface.
While different chemicals can be used for electropolishing, the most common include acidic electrolytes like sulfuric acid or phosphorus acid. The highly acidic nature of these chemicals allows it to quickly and efficiently eat away at the surface of metal objects. Some manufacturing companies use other metals, such as perchloric acid or various acid mixtures but most use either sulfuric acid or phosphorus acid when performing electropolishing.
Electropolishing vs Electroplating: What’s the Difference?
Electropolishing and electroplating are both electrochemical processes that involve the application of chemical and electricity to a metal object. However, they work in opposite ways. Electropolishing levels the surface of a metal object to make it smoother and more uniform, whereas electroplating dissolves metal ions to trigger the formation of a new metal layer over the object.
Advantages of Electropolishing
- Improves the appearance and aesthetics of the finished workpiece.
- Makes metal workpieces more resistant to corrosion and rusting.
- The smooth surface created by electropolishing makes the metal workpiece easier to clean and sanitize, which is essential for certain applications like healthcare.
- Reduces friction created on the surface of metal workpieces.
- Don’t lower or otherwise affect the strength of metal workpieces.
- Can be used to increase the magnetism of metal workpieces.
- It’s a relatively lost-cost electrochemical process.
- In addition to creating a smoother surface, electropolishing can make metal workpieces smaller.
- Several standards are available for electropolishing, including ASTM E1558, ASTM B 912-02, ASME BPE and ISO.15730.