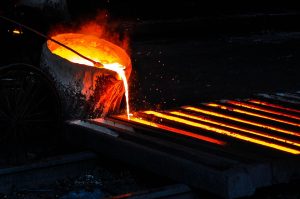
Over the past 50 years, global production of steel has increased by over 300%, jumping from just 500 million tons during the 1960s to over 1,600 million tons in 2016. Steel, of course, is just one of many metals produced and sold. Others include titanium, copper, brass, aluminum and more. While the exact process used to produce these metals varies, many metalworking companies use rolling in their production method.
What Is Rolling in Metalworking?
In metalworking, rolling is a forming process that involves feeding molten metal through two or more rollers. A metalworking company first heats the metal in a large furnace until it achieves a molten state. Depending on the type of metal, this may require temperatures of 2,500 degrees Fahrenheit or higher. After the raw metal has been melted, it’s fed through one or more rollers.
Why Metal Is Rolled
Rolling offers several benefits, one of which is a thinner size. As the molten metal is fed through the rollers, it becomes compressed and, therefore, thinner. For certain applications, such as the production of sheet metal, this is critical to creating the finished product. If the molten metal isn’t compressed, it will be too thick for its intended purpose or application.
In addition to making metal thinner, rolling also promotes a more uniform shape. From top to bottom and edge to edge, all rolled metal has the same shape. Therefore, metalworking companies don’t have to worry about some parts of the metal being thicker than other areas.
Hot and Cold Rolling: What’s the Difference
Rolling processes can be classified as either hot or cold. Upon reading the terms “hot rolling” and “cold rolling,” you may assume that the former involves feeding molten metal through rollers and the latter involves feeding cold or room-temperature metal through rollers. However, this isn’t necessarily the case.
Hot rolling consists of the same steps previously mentioned. Cold rolling, on the other hand, consists of these same steps but with an added step at the end. With cold rolling, the hot-rolled metal is moved to a separate forming station where it’s rolled once more. This time, however, it’s rolled at room temperature.
Because cold rolling involves compressing metal while the metal is below its recrystallization temperature, it changes the physical properties of metal. Metal that’s been cold rolled is typically stronger and able to hold tighter tolerances than hot-rolled-only metal. The downside, of course, is that cold rolling requires more time and resources than hot rolling.