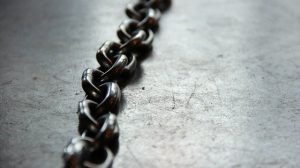
Metal is oftentimes manipulated after being smelted from raw ore to improve its strength, durability, ductility or other physical properties. While most of these metalworking processes involve the use of heat, others do not. Cold working, for example, is a group of metalworking processes that’s designed to improve the physical properties of metal at or near room temperature. What is cold-worked metal exactly, and how does it differ from other metalworking processes?
Overview of Cold-Worked Metal
The term “cold-worked metal” refers to any metal workpiece that’s been physically manipulated below its respective recrystallization temperature. All metals have a specific temperature at which they develop new grains. Known as a recrystallization temperature, it occurs at hot temperatures. Steel, for instance, has a recrystallization temperature of about 750 to 1,300 degrees Fahrenheit. Cold working simply involves reshaping a metal workpiece below this temperature, with most cold-working processes occurring at or near room temperature.
The 4 Main Cold-Working Techniques
There are four main cold-working techniques that companies use to manipulate metal workpieces at or near room temperature: squeezing, drawing, shearing and bending. Each technique involves a different approach. Squeezing, for instance, involves compressing a metal workpiece between two or more rollers, whereas shearing involves cutting a metal workpiece with a straight cutting blade. Regardless, all four techniques allow companies to manipulate the shape and/or size of a metal workpiece while keeping the workpiece at or near room temperature.
Cold-Worked vs Hot-Worked Metal
Metal can be classified as either cold worked or hot worked, depending on the temperature at which it was manipulated. If a metal workpiece is manipulated at or near room temperature, it’s considered cold worked. If it’s manipulated at a temperature above the metal’s recrystallization point, on the other hand, it’s considered hot worked.
Advantages of Cold-Worked Metal
Cold-worked metal is often preferred because of the advantages it offers over hot-worked metal. While hot-working processes can change the size and shape of metal workpieces, it comes at the cost of strength. Exposure to heat typically makes metal workpieces weaker. As a result, cold-working processes are used in applications requiring a strong finished product.
Not only does it offer increased strength, but cold working is also easier to perform. Without the need for heat, companies can perform cold-working processes more quickly than hot-working processes. Therefore, cold-worked metal typically costs less to produce than its hot-worked counterpart.