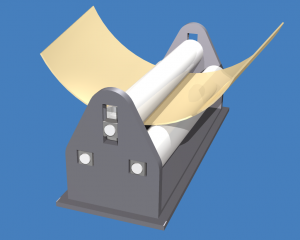
Not all manufacturing applications require the use of flat metal. Some require the use of warped metal. For applications such as this, the raw sheet metal must be deformed using a bending process. In metalworking, bending refers to the deformation of an otherwise flat piece of metal, causing it to bend either up or down in one or more areas. Below are some of the most common bending processes and how they work.
Air Bending
Air bending is a bending process that involves the use of a punch brake to bend sheet metal. Once positioned inside the punch press, the top die presses down and into the bottom die. Because the sheet metal is positioned between these two dies, it bends to form the shape of the dies.
Coining
Also using a press brake is the bending process known as coining. Coining is a high-performance bending process that’s characterized by greater force. Like air bending, it compresses sheet metal between a top die and a bottom die. The difference between these two processes is that coining uses up to 30 times more pressure to bend sheet metal than air bending, making it highly useful for bending thick and/or hard sheet metal.
Bottoming
Bottoming is a bending process in which sheet metal is pressed against a bottom die featuring a V shape. While other bending processes typically support the use of both U- and V-shaped dies, bottoming only uses a V-shaped die. It’s often preferred over air bending because of its higher level of accuracy as well as less recoil with the finished sheet metal.
Roll Bending
As shown in the image above, roll bending is a more rudimentary bending process that involves the use of multiple rollers to bend sheet metal. It’s typically performed using a roll bender with three separate rollers. One roller is placed at the top, whereas the remaining two rollers are positioned directly underneath the top roller. When sheet metal is fed through the rollers, it bends
3-Point Bending
Finally, three-point bending is a relatively new bending process that requires the use of an adjustable die. Unlike with other bending processes, the bottom die isn’t fixed in a stationary position. Rather, the bottom die used in three-point bending features an adjustable height. It can be raised or lower, allowing for a greater level of versatility. Like coining, though, three-point bending is a more costly bending process compared to other bending processes.