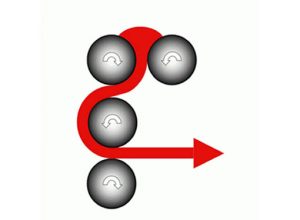
Calendaring is a finishing process used in the manufacturing industry to create high-performance rubber, as well as other materials, for use in products such as gaskets, seals and O-rings. Rather than using standard rubber to produce products such as these, manufacturing companies often use calendared rubber. Both standard rubber and calendared rubber still consist of the same basic rubber material, but the latter type offers several advantages over its counterpart.
What Is Calendaring?
No, calendaring doesn’t refer to keeping track of dates using a 12-month calendar. It refers to a process in which rubber or other materials is forced between multiple rotating rollers. It’s essentially an ironing process that smooths out rubber as it’s forced between the rollers under pressure. Depending on the specific type of calendaring machine, as well as the number of rollers used in the process, it may exert up to 500 pounds per square inch (PSI) of pressure on the rubber.
Calendar doesn’t rely strictly on pressure to perform this task, however; it also uses heat. Some or all of the rotating rollers used in this finishing process are heated, meaning the rubber is naturally heated as it’s forced between the rollers. Heat causes the rubber to deform, making it more pliable.
Increased Strength
Calendaring can increase the strength of rubber by compressing it. As previously mentioned, some calendaring processes produce up to 500 PSI of pressure. When exposed to such extreme pressure, rubber compresses, thereby becoming stronger and more durable.
Smooth Finish
Calendaring also allows for a smooth finish. Using both heat and pressure, calendaring machines can smooth out any lumps or imperfections on the surface of rubber. Once the sheet of rubber exits the calendaring machine and has cooled off, it will have a silky-smooth texture that’s not possible using other finishing processes.
Control of Thickness
Finally, calendaring can be used to produce sheets in rubber with a specific thickness. For products such as gaskets and seals, this is critical to their manufacturing process. If a gasket or seal is too small, it may leak. But manufacturing companies can easily create gaskets and seals with a specific thickness using calendaring. The thickness of calendared rubber is controlled by adjusting the distance between the rotating rollers. Moving the rotating rollers farther apart from each other results in thicker calendared rubber, whereas moving the rotating rollers closing together results in thinner calendared rubber.
No tags for this post.