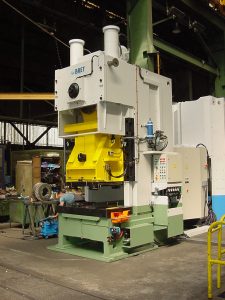
Not to be confused with metal fabrication, metal stamping is a metalworking process that involves the use of an industrial machine to deform a flat sheet of metal into a specific shape. Using pressure, the machine compresses the sheet metal against a die surface. This changes the shape of the sheet metal to reflect that of the die surface.
History of Metal Stamping
Metal stamping has been around for over a century. In Germany during the 1880s, the process was used extensively by bicycle manufacturers to create components like frames and handlebars. Shortly thereafter, companies in the United States began using metal stamping for other purposes. The Ford Motor Company, for example, is said to have used metal stamping to produce car parts after discovering the high resource cost of using forged parts.
The Inner Works of Metal Stamping
By definition, metal stamping is a relatively simple process in which sheet metal is pressed against a die surface using a stamping press. However, there are different steps to achieving this goal. In some cases, sheet metal is initially too large for the process, so it must be trimmed down using a process known as blanking. With blanking, large sheet metal is cut into smaller pieces for use in metal stamping.
Depending on the type of stamping process used, the sheet metal may also require piercing. If the stamping press features rods in which the sheet metal is placed, the metal must be pierced so that the rods can slide through it.
Blanking and piercing are optional steps in metal stamping. Regardless of whether they are performed, a stamping press is eventually used to physically manipulate and deform the sheet metal into the shape of the die surface.
Benefits of Metal Stamping
Metal stamping is an easy and effective way to change the shape of sheet metal. There are even computer-controlled (CNC) stamping presses that allow manufacturers to design their desired metal shape in a computer program.
Manufacturers can use metal stamping to achieve complex and intricate shapes that aren’t possible with other metalworking processes. As long as the right die shape is used, metal stamping will turn a conventional sheet of metal into the desired shape.
It’s also worth noting that metal stamping is typically performed using cold sheet metal, meaning manufacturers aren’t required to heat up or smelt their metal as required in other metalworking processes. Along with the other benefits listed, this is one more reason why manufacturers use metal stamping.
If you like this check out our article on metal spinning.