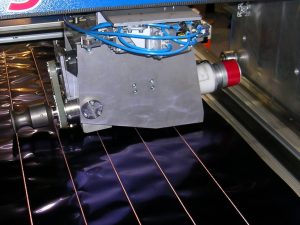
Not all welding processes involve the use of an electric arc. While arc welding is certainly popular in the manufacturing and construction industries, there are welding processes available, including ultrasonic welding. Unlike arc welding, ultrasonic welding doesn’t use electricity to join two or more materials together. It uses ultrasonic sound waves. To learn more about the science behind ultrasonic welding and how this modern welding process works, keep reading.
What Is Ultrasonic Welding?
Ultrasonic welding is a welding process that’s characterized by the use of ultrasonic sound waves. Originating in the 1940s, it creates sound waves that vibrate to produce heat. When two objects are exposed to the vibrating ultrasonic sound waves, they’ll warm up. As the temperature of the objects increases, they’ll join together.
During ultrasonic welding, pressure is applied to the objects intended to be joined. Normally, a pneumatically powered press is used for this purpose. The press squeezes the objects while exposing them to ultrasonic sound waves. The ultrasonic sound waves, of course, are responsible for creating heat through vibrations. The combination of both heat and pressure allows the objects to join together.
Ultrasonic welding has become increasingly popular among automakers. In the late 1960s, a car was made entirely out of components using ultrasonic welding. Since then, automakers throughout the world have integrated ultrasonic welding into their manufacturing operations. With that said, ultrasonic welding is used in countless other applications as well.
The Benefits of Ultrasonic Welding
When compared to other welding processes, ultrasonic welding offers several benefits. First and foremost, it supports a variety of materials. Whether an object is made of plastic or metal, it can probably be joined with another object of the same material using ultrasonic welding. When performed on metal objects, ultrasonic welding uses a temperature that’s below the metal’s melting point. As a result, it doesn’t alter or otherwise change the metal’s physical properties.
Most importantly, ultrasonic welding doesn’t require the use of solder, adhesives or welding rods. It’s a fastener-free welding process that’s used to create clean bonds. This alone is reason enough for manufacturing companies to consider ultrasonic welding over other welding processes.
The downside to ultrasonic welding is its high startup cost. While the process itself is relatively cheap, the equipment required to perform ultrasonic welding is expensive. Therefore, it’s generally used by large manufacturing companies who have the funds necessary to purchase the ultrasonic welding equipment.