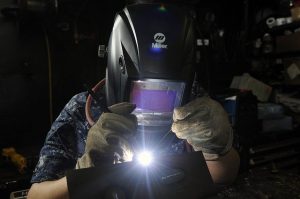
Have you heard of induction welding? It’s a high-frequency welding process that involves the use of an electromagnet to generate heat. With induction welding, radio-frequency electricity powers an induction coil. As the induction coil receives the electrical current, it heats up. The induction welding apparatus can then be used to weld two or more objects together by melting their respective surfaces. Below are the top 5 benefits of induction welding.
#1) Efficiency
Although it requires electricity, induction welding is a highly efficient welding process. It requires less electricity than other high-frequency welding processes, making it an attractive choice for large-scale welding applications, such as those performed by manufacturing companies. The apparatus using in induction welding is powered by electricity, but don’t let that fool you into thinking it consumes a substantial amount of electricity. Induction welding is an efficient welding process that generally consumes less electricity than other welding processes.
#2) Focused Heat
In addition to efficiency, induction welding is capable of producing focused heat. In other words, the heat created by the induction welding apparatus is localized to a single and specific area, thereby protecting the workpiece from damage. This alone makes induction welding an attractive choice for pipes. Water and plumbing pipes are often joined at the seams using the induction welding. The focused heat joins the pipes together at the seams without damaging them.
#3) Supports a Variety of Materials
From iron and steel to plastic and composites, induction welding supports a wide variety of materials. Both ferrous and nonferrous metals can be welded together using this modern welding process. If a material is nonmagnetic, such as plastic, it’s typically implanted with ferrous compounds, thereby allowing the material to absorb the electromagnetic energy produced by the induction welding apparatus. As long as the material contains ferrous compounds, it can be welded using an induction welding apparatus.
#4) Removes Impurities
You might be surprised to learn that induction welding can remove impurities from workpieces. During this high-frequency welding process, the workpiece heats up when exposed to the induction welding apparatus. As the respective surfaces of the workpieces are pressed together, impurities are forced out of them. In turn, induction welding offers cleaner workpieces — once they’ve been welded — than that of other welding processes.
#5) Automation
While it can’t be completely automated, many steps in the induction welding process can be performed automatically to streamline a manufacturing company’s operations. Load matching, for instance, can be automated to achieve an appropriate amount of power to heat and weld the workpieces.