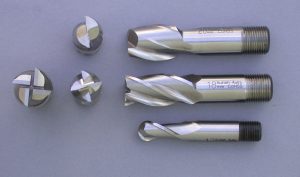
A milling cutter is an essential component of a milling machine. As the name suggests, it’s the cutting tool that’s responsible for scraping material out of a workpiece. All milling machines have a cutter. During a typical milling operation, the cutter moves perpendicular to its axis, allowing it to remove material from the workpiece on the circumference of the cutter. To learn more about milling cutters and how they work, keep reading.
Overview of Milling Cutters
The purpose of a milling cutter is to remove material from a workpiece. With that said, milling cutters don’t consist of a single blade. While turning operations performed using a lathe generally feature a single-bladed cutting tool, milling cutters consist of multiple blades. As the milling cutter rotates against a stationary workpiece, it scrapes out material.
Milling cutters are often made of hard, strong materials that can withstand significant stress without breaking or otherwise succumbing to damage. For example, it’s not uncommon for milling cutters to feature a coating of polycrystalline diamond (PCD). According to Wikipedia, PCD-coated milling cutters last up to 100 times longer than their uncoated counterparts. The download to using PCD-coated milling cutters is that they can’t be used in applications where the temperature exceeds 1,112 degrees Fahrenheit.
The Different Types of Milling Cutters
All milling cutters are characterized by the presence of multiple grooves, each of which acts as a blade that scrapes out material from the workpiece. With that said, there are different types of milling cutters. An end mill cutting tool, for instance, is a type of milling cutter that has teeth on the end and the sides. Available in steel and cement carbide materials, they are typically used in vertical milling operations.
Another common type of milling cutter is a rough end cutter. Rough end cutters have deep grooves on the end that are capable of removing an excess amount of material from the workpiece. Also known as ripper cutters, rough end cutters are typically used in high-volume manufacturing applications.
A third type of milling cutter is a ball cutter. Also known as a ball end cutter, a ball cutter features a hemispherical design that minimizes stress on the workpiece.
Finally, a side-and-face cutter is a type of milling cutter that has teeth on the side and front. Side-and-face cutters have been around since the early 1800s. Back then, in fact, they were the most common type of milling cutter.
A milling cutter is an essential component of a milling machine. Consisting of multiple blades, it’s responsible for scraping material out of a workpiece, thereby reshaping the workpiece.