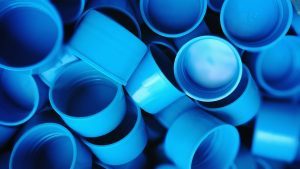
From bottle caps and kids’ toys to patio chairs and small gears, plastic injection molding is used to make a variety of consumer products. It’s a highly effective, and efficient, way to produce large volumes of plastic products. After creating a mold, manufacturing companies can use it to produce countless products in that same size and shape. But what exactly is plastic injection molding?
Plastic Injection Molding Explained
Plastic injection molding is a molding process characterized by the use of thermoplastics. In general, molding supports many different materials, some of which include glass, metal and elastomers. Plastic injection molding, however, specifically uses thermoplastic as the raw material that’s poured into a mold.
While it has undergone numerous improvements and changes since, plastic injection molding has origins dating back to the 19th century. In 1872, brothers John and Isaiah Wyatt patented the first injection molding machine, which they used to inject heated plastic into a mold.
What Is Thermoplastics?
Also known as thermosoftening plastics, thermoplastics are polymer materials that temporarily become softer and more pliable when exposed to heat. During plastic injection molding, thermoplastic material is heated until it turns from a solid state to a liquid state, at which point it’s poured into the mold. Thermoplastics are ideal for injection molding because of their ability to become pliable when exposed to heat. Furthermore, excess thermoplastic material can be easily recycled, thereby reducing waste for manufacturing companies.
How Plastic Injection Molding Is Performed
Before plastic injection molding can be performed, a mold must first be created. Common materials used to make molds for plastic injection molding include stainless steel, high-carbon steel and aluminum. For high-volume applications, though, steel is preferred because of its superior strength and resistant to wear than that of aluminum. Steel molds can easily last for hundreds of thousands of applications, making them a cost-effective solution for manufacturing companies that produce large volumes of plastic products.
Once the mold has been created, thermoplastic material in the form of small pellets are fed into a large drum-like barrel where they are heated and pushed sideways towards the mold. As the injection molding machine’s screw pushes the liquefied material, the material eventually reaches a nozzle that further pressurizes and pushes the thermoplastic material into the mold.
Next, the liquified thermoplastic material is cooled — typically at room temperature — until it hardens. Depending on the type of injection molding machine used, it may feature a platen that opens after the material has cooled, allowing for the removal of the newly created plastic product.