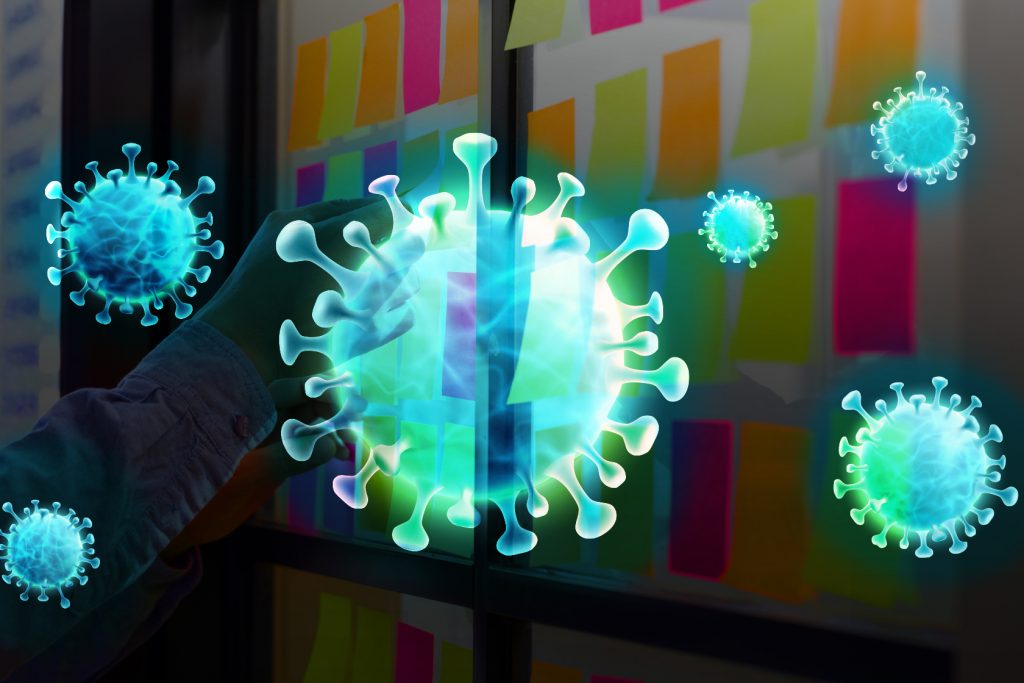
Most Americans are not familiar with the business model that delivers their groceries. In fact, “supermarkets” were the source for most of the good practices that have evolved into “just in time manufacturing”. The term “Kanban” evolved from grocery stores to also define the process by which manufacturers only bought components “as needed” or “just in time” to make things like cars.
When interest rates and the cost of money were high it made sense for companies like Toyota, Ford, and GM to avoid the cost of inventory by only receiving parts as needed thus installing a pull system where suppliers are burdened with matching demand and production. Kanban really took hold in the 90’s and drove good practice in a lot of ways. Purchasing systems became more robust, and suppliers were driven to find efficiencies. In the end, by pushing inventory cost- control upstream to suppliers, the big manufacturers lowered cost through the innovation it demanded at the supplier level. The advent of cheap money and variations in the economy never outweighed the benefits of the system.
This discussion began with one of my friends asking why there was no toilet paper to be found. My first answer of course was that there was plenty of toilet paper- inventoried in their neighbors closet. In manufacturing terms, toilet paper went from a vendor managed inventory item to an end user stockpile. Why? Toilet paper is relatively cheap so carrying a stockpile does not hurt your household business model. The “cost of inventory” was fairly low. People were not hoarding cars, boats, or home improvement products. It is a testimony to the “just in time” system we have built in manufacturing that there is now and will be toilet paper on the shelves. The “inventory” pull on toilet paper is over…use did not increase…the system prevailed.
The short answer to all of us in manufacturing is that Covid-19 will not kill Kanban, good practice, or Vender Managed Inventory programs. Manufacturing distributors like Monroe Engineering are the shock absorbers for the system. Driven to good practice by our customers; we are part of a global supply chain that works. So don’t worry too much about getting your spring plungers, hinges, or even ventilator parts. Covid-19 will not kill the good practice of “just in time Inventory”. More importantly, it is showing just how strong our global supply chain really is.