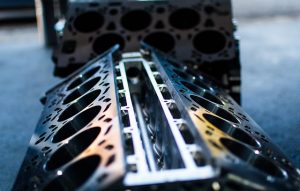
Manufacturing companies often use die casting produce complex metal products and components with precise dimensions. There are other processes available that can manipulate metal workpieces into a new size and shape. Die casting, however, is more accurate since it allows for close tolerances and precise dimensions. Below are five fun facts about the manufacturing process die casting.
#1) Uses Molten Metal
While die casting can be performed in different ways, all die casting processes require the use of molten metal. During this manufacturing-related casting process, molten metal is injected into a mold cavity. The metal is first heated until it converts from a solid to a liquid state, after which it’s forced into the interior cavity of a mold.
#2) Invented in the 1800s
Die casting may sound like a relatively modern casting process, but it’s actually been around for several centuries. Some of the first die casting processes emerged during the early to mid-1800s in the printing industry. Shortly thereafter, the United States Patent and Trademark (USPTO) granted a patent for a small and portable die casting machine. Die casting has since increased in popularity, with manufacturing companies across the world using it to produce metal products and components with precise dimensions.
#3) Supports Many Metals
Along with its precise dimensions, die casting supports a wide variety of metals. Aluminum is commonly used in die casting because of its unique properties. It’s lightweight, inexpensive and liquefies at a relatively low temperature. Other metals used in die casting include zinc, steel, magnesium, copper, lead and brass. Each metal, of course, has its own properties, so manufacturing companies must consider the type of metal used when performing die casting.
#4) Cold and Hot Die Casting
There are two primary forms of die casting: cold and hot. Considering that they both involve forcing molten metal into a die casting, the terms are somewhat confusing. After all, cold die casting still uses molten or “hot” metal. The difference between them is that cold die casting uses a separate chamber to heat up the raw metal, whereas hot die casting heats up the raw metal within the same machine.
#5) Requires Preparation
Die casting requires preparation to ensure a positive outcome for the finished product or component. When preparing the mold cavity, for example, manufacturing companies must apply lubricant to the interior walls. Lubricant servers several purposes. It helps to lower the temperature of the die cavity while also allowing the metal casting to be easily ejected or removed.