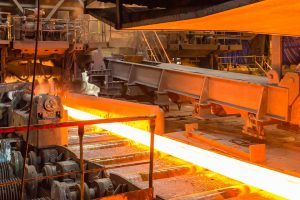
In metalworking, rolling involves forcing metal — either cool or heated — through one or more rollers to change the metal’s physical properties. The rollers compress bar or sheet metal, thereby making it thinner while also achieving a more uniform size and shape. Not all metal rolling is the same, however. There are different types of metal rolling processes, each of which has a specific function.
Roll Bending
Roll bending involves the use of three rollers, two of which are located on the bottom, to press and shape metal into an arc. The rollers are affixed to three axes, allowing just enough space between the two bottom rollers and the single top roller for the respective bar or sheet metal to enter. As the bar or sheet metals is fed through the bender machine, the rollers deform it to produce the shape of an arc.
Roll Forming
Roll forming is a more complex rolling process that involves the use of nine different rollers to create complex shapes. Roll forming machines have three sets of rollers, the first of which consists of four rollers; the second consists of three rollers; and the third consists of just two rollers. Each set of rollers deforms the sheet metal in a different way, allowing for the creation of complex shapes that aren’t achieved through other rolling processes.
Ring Rolling
While most rolling processes involve the use of cold metal, ring rolling specifically requires heated metal. With ring rolling, a cylinder of heated metal is placed between two rollers. When the rolling machine is activated, the rollers compress the heated metal cylinder while simultaneously reducing its diameter size. Ring rolling is used in a variety of manufacturing applications, some of which include the production of copper pipes, mechanical gears, bearings and fasteners. It’s particularly effective because it requires heated the metal before feeding it through the machine’s rollers.
Flat Rolling
The most common type of metal rolling process is flat rolling. Flat rolling machines contain just two basic rollers. One roller is found on top, whereas the second roller is located on the bottom. The bar or sheet metal is fed through the middle of these two rollers, which compresses it into a smaller and more uniform shape. It’s important to note that the rollers used in this process rotate in different directions. The alternating directions of the rollers allows the machine to deform the metal without simply pushing it through.