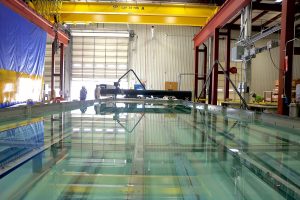
There are other ways to cut metal besides using a shear blade. Water jets cutting, for example, refers to the use of a specialized tool that blasts metal — or other hard materials — with a stream of high-pressurized water. Whether it’s aluminum, copper or steel, most metals can be cut using this method.
Origins of Water Jet Cutting
Water jet cutting has origins dating back to the mid-19th century, during it which it was used for mining operations. Back then, mining companies would blast rock and sediment materials with water to dislodge them. With that said, it wasn’t until the 1930s when water jets became narrow enough to use in the manufacturing industry. The advent of narrow water jets allowed manufacturing companies to easily cut a variety of materials, including metal, using high-pressurized water.
How Water Jet Cutting Works
How does water jet cutting work exactly? There are different types of water jets, each of which work in different ways. Most, however, rely on a similar principle of blasting metal with a high-pressure stream of water. The water jet machine is connected to a high-pressure pump, which pressurizes the water using hydraulic oil. As the water is pumped through the narrow tubing, it’s propelled out the nozzle through a small hole. To put the power of water jet cutting into perspective, it’s not uncommon for water jets to blast water at a speed of roughly 2,500 feet per second. At this speed, water jet cuts are able to cut through even the hardest materials.
Benefits of Water Jet Cutting
Although there are numerous ways to cut metal, water jet cutting offers several noteworthy benefits, one of which is it’s ability to cut metal without producing heat. Most other cutting operations create heat. Even using a shear will produce heat from friction. And this heat may alter the physical properties of the metal. Water jet cutting, on the other hand, ensures the metal workpiece remains cool while it’s being cut.
Water jet cutting is also incredibly accurate. When performed correctly, it’s able to achieve a cutting accuracy of approximately 13 millimeters. Other cutting methods lack this level of accuracy, making water jet cutting an attractive choice among manufacturing companies.
Water jet cutting machines can even be controlled using computer numerical control (CNC). With a CNC water cutting machine, manufacturing companies can program the cutting operations in a computer program, allowing for streamlined cutting processes.